Pcb Assembly Reflow Soldering Temperature Control Requirements
Ensuring that the temperature curve of the reflow soldering process meets the temperature requirements of the product and ensuring the soldering quality of the pcb assembly manufacturing product. This guideline applies to all reflow soldering temperature control in our SMT workshop.
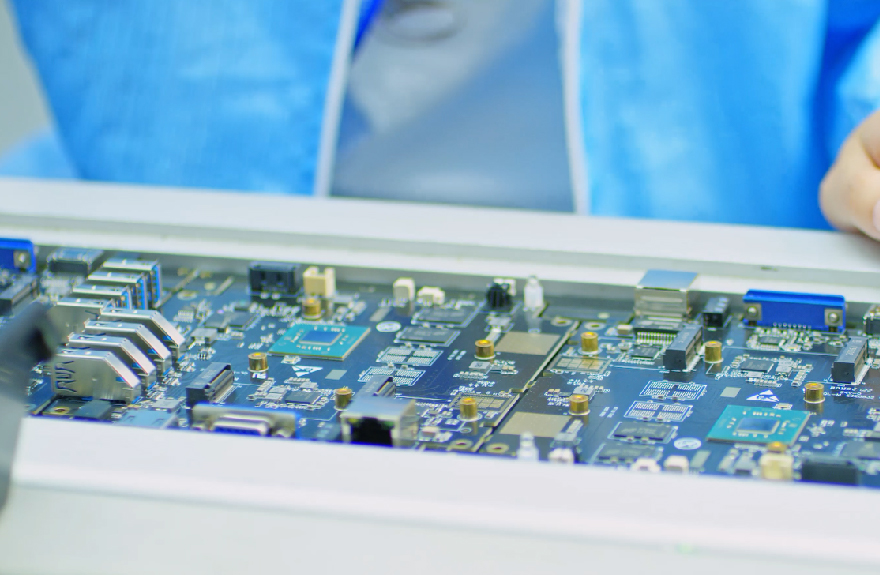
Reflow soldering temperature control requirements
1. After reflow soldering, the temperature in each temperature zone should be stable and the chain speed should be stable before through furnace and test temperature curves can be carried out. The temperature from the cold start machine to the stable temperature is usually 20~30 minutes.
2, The production line technicians must record the furnace temperature setting and chain speed every day or every product, and regularly carry out the furnace temperature curve measurement controlled text test to monitor the normal operation of the reflow soldering. IPQC conducts inspection supervision.
3. Lead-free solder paste temperature curve setting requirements:
3. 1 The setting of the temperature curve is mainly based on: A. The recommended curve provided by the solder paste supplier. B. PCB material, size and thickness. C. The density of components and component size.
3.2 Lead-free furnace temperature setting requirements:
3.2. 1. Within 100 points of mounting points, there are no BGA and QFN and other pin ICs and products with pad sizes below 3MM. The measured peak temperature is controlled at 243 to 246 degrees.
3.2.2, the number of mounting points is over 100, there are products with dense pin IC, QFN, BGA and PAD size below 3MM and 6MM, the measured peak temperature is controlled at 245 to 247 degrees.
3.2.3, there are more dense foot IC, QFN, BGA or PCB board thickness of 2MM (inclusive) or more, PAD size is more than 6MM individual special PCB board products, according to actual needs, the measured peak temperature is controlled at 247 to 252 degrees .
3.2.4, FPC soft board and aluminum substrate and other special substrate or parts with special requirements, need to be adjusted according to actual needs (product process description is special, according to process description control)
Remarks: SMT technicians and engineers are immediately fed back when there is an abnormality in the actual operation of the product.
3.3 Basic requirements of the temperature curve
A. Preheating zone: The preheating slope is 1~3°C/SEC, and the temperature is raised to 140~150°C.
B. Constant temperature zone: 150°C~200°C, maintained for 60~120 seconds
C. Reflow zone: above 217 ° C for 40 ~ 90 seconds, peak 230 ~ 255 ° C.
D. Cooling zone: The cooling slope is less than 1~4°C/SEC (in which PPC and aluminum substrate are removed, the actual temperature should be determined according to the actual situation)
Precautions:
1.The first five circuit board post-furnace are to be inspected for the gloss, tin absorption and weldability of each circuit board.
2. Model using control: using solder paste strictly in accordance with the "Product Process Description" and customer requirements.
3. The temperature of each furnace is required to be tested per shift, and test again for changing shift. The trial production model requires each model to best tested once, When adjusting the quality of the road, it is necessary to confirm whether there are any circuit board or other abnormal objects in the furnace. And confirming that the width of the import and export is the same.
4. Each time the temperature parameter changes, the furnace temperature needs to be tested.
Article keywords :Pcb,Assembly,Reflow,Soldering,Temperature,Control,Ensuring,